プラスチック成形に欠かせない射出成形金型|金型の種類とその特徴は?
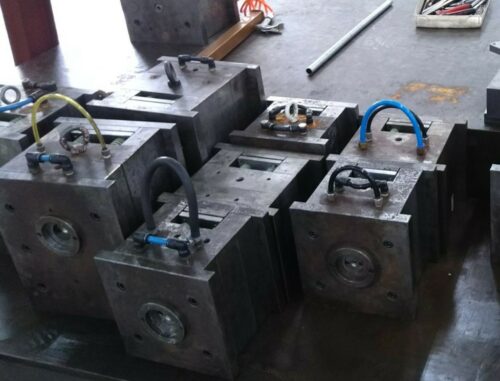
目次
金型とは?
「金型」とは、素材の塑性や流動性を利用して加工するための、金属製の型をいいます。金型は通常、凸型の「コア(Core)」と凹型の「キャビティー(Cavity)」とから構成されます。両型の接触面を正しく合わせることにより空洞ができ、この空洞内に材料を注入することで成形品が完成します。
金型の種類
金型は、プラスチック成形のほか、金属板のプレスや鍛造、鋳造(鋳物)などに用いられます。金型には、次のような種類があります
・プラスチック用金型
射出成形用、圧縮成形用、真空成形用などがある。樹脂ペレットから、家電製品、OA機器、自動車、雑貨などの部品を製造するのに使用。
・プレス用金型
プレス加工に用いられ、抜き型、曲げ型、絞り型、圧縮型などに分類。鋼板や非鉄金属などを材料として、自動車用部品、家電製品用部品、雑貨用部品などの製造に使用。
・鍛造用金型
熱間鍛造用、冷間鍛造用などがある。棒網材、非鉄金属などの材料から、自動車用部品(クランク軸など)、オートバイ用部品、ジェット機用部品(ファンなど)、建設機械用部品などを製造するのに使用。
・鋳造用金型
シェルフモールド、ロストワックス、重力鋳造、圧力鋳造などの鋳造に利用される金型。アルミ合金などの材料から、工業用部品、建設機械用部品、農業機械用部品などを製造するのに使用。
・ダイカスト用金型
鋳造用金型の一種であり、熱衝撃や熱疲労に耐えられるように、特殊な合金鋼からできている。軽合金や亜鉛合金などを材料として、自動車用部品(エンジン回りの部品など)、精密機械用部品(カメラのボディーなど)、電機製品用部品(電動工具のボディーなど)などの製造に使用。
・ガラス用金型
ガラス材料を押型や吹型により成形し、瓶やボトル、照明器具用部品、食器などを製造するのに使用。
・ゴム用金型
合成ゴムまたは天然ゴムを材料として、工業用部品、自動車用部品、タイヤ、履物などの製品に使用。
・粉末冶金用金型
金属粉末を注入して固め、焼結して製品を作る。多孔質の含油軸受、歯車、電気接点などの機械部品、焼結磁石、サーメットなどの製造に広く使用。
プラスチック加工に欠かせない「射出成形金型」
プラスチック用金型には、射出成形用をはじめとする金型があります。
射出成形は、生産性が高いため、プラスチックの加工法として世界中で広く用いられています。「射出成形」とは、射出成形機のシリンダー内で加熱溶融させた樹脂材料を、高速かつ高圧で金型内に流し込み、冷却固化または加熱硬化させて成形品を得る方法です。
関連記事「試作アルミ型でのPlaQuick射出成形」はこちら
プラスチック加工の世界では、成形品の品質、生産性を左右する要素として、材料、金型、成形機があります。中でも、金型は、”製品の産みの親”と言われることがあり、その良しあしは製品の良否に直結しています。
こうしたことから、射出成形を良好に実現するためには、性能に優れた射出成形金型が必要となります。
関連記事「プラスチック(樹脂)の成形方法や成形メカニズムについて徹底解説!」はこちら
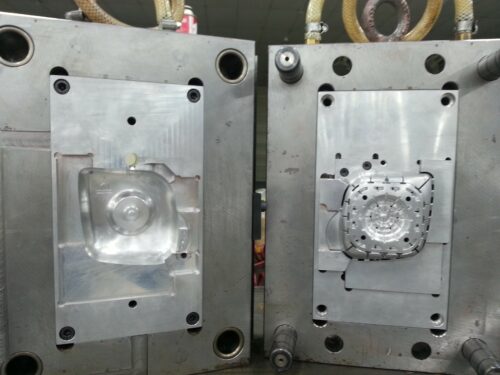
射出成形金型の種類
射出成形金型は、大きくは、「コールドランナー金型」と「ホットランナー金型」とに分類されます。それぞれの概要を以下に示します。
コールドランナー金型
成形時にランナー(射出成形機内にある、金型への溶融樹脂の通り道)を冷やし、製品部分とともに取り出されるように設計された金型。ランナーと製品部分がともに同じ金型の分割面(パーティングライン)から取り出される「2プレート金型」と、ランナーと製品部分がそれぞれ別の分割面から取り出される「3プレート金型」とに大別される。
ホットランナー金型
ランナー部分の樹脂を固化しないようにする(溶融したままにする)ことにより、ランナーを取り出さず連続して成形できるように設計された金型。ランナーレス金型とも呼ばれる。
射出成形金型を使った成形の流れ
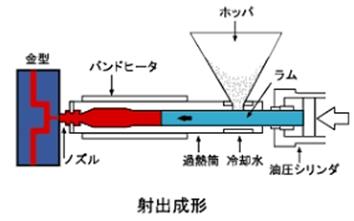
射出成形によって成形品ができるまでの流れは、次表のとおりです。工程は(1)~(6)の順に進行し、射出成形金型の取り扱いが重要となります。
(1)樹脂を溶かす
シリンダーで樹脂ペレットを溶かす工程
(2)型閉じ(型締め)
金型を閉じる(締める)工程
(3)射出・保圧
金型に注入された溶融材料の冷却固化に伴う収縮を補うために、所望の圧力で所望の時間をかけて溶融材料を金型に補充する工程
(4)保圧・冷却
寸法、物性などが安定し取り出し可能となる温度域まで、成形品を冷却固化する工程。冷却固化は、溶融材料から金型への熱移動によって起こる。
(5)型開き
成形品を取り出すために、所望の位置(型開き位置)まで金型を開く工程
(6)製品取り出し
プレート・ピンを介して、成形品を押し出す(突き出す)工程
射出成形のメリットとデメリット
射出成形は、生産性が高い反面、金型の製作にコストと時間がかかります。以下に、射出成形のメリットとデメリットを挙げます。
射出成形のメリット
- 複雑な形状、さまざまなサイズの製品を作ることができる
- 後加工(バリ取りなど)が少なくて済む
- 成形サイクルが短く、大量生産が可能
- 寸法精度が高い
- 生産工程の自動化を図りやすい
射出成形のデメリット
- 金型の製作コストが高くなることが多い
- 少量生産には不向き
- 極端な肉厚化、薄肉化が難しい
おわりに
ご説明してきましたとおり、金型には、素材や加工方法に応じて、さまざまな種類があります。これらの中でも、射出成形金型は、プラスチック成形用に特化されたものです。射出成形金型の性能が成形品の品質に影響を及ぼすといっても過言ではありません。
PlaQuickでは試作アルミ型による射出成形を短納期、低コストで行っています。試作でお困りの際には、ぜひお問合せ下さい。