プラスチック(樹脂)の成形方法や成形メカニズムについて徹底解説!
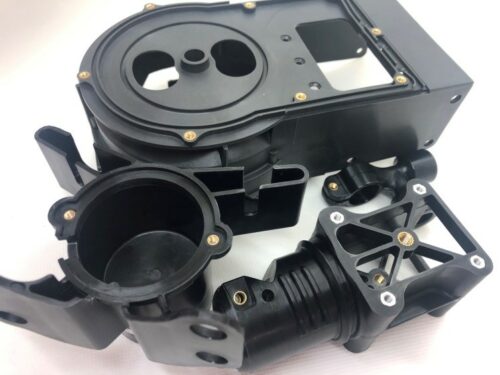
\ 図面は不要!たった1分で完了! /
目次
プラスチック(樹脂)の成形とは?
プラスチックは材料を溶融・固化という工程を行うことで成形され、金型によって設計通りの形状を得ることができます。私たちの身の回りの製品には成形されたプラスチックが数多く使用されており、自動車部品から食品の包装容器、家電製品、航空機などに活用されています。
自動車部品など複雑な形状のものを金属で加工しようとすると時間がかかるうえにお金もかかりますが、プラスチックなら複雑な形状でも効率的に生産できるため大量生産に向いているのが特徴です。それ以外に軽量化やコスト削減などにも貢献できるというメリットがあります。
プラスチックは、使用環境や成形条件によって影響を受けやすい性質を持っています。特にプラスチックは熱によって膨張や収縮をしやすく、設計の段階で使用環境の温度を考慮しないと目的の寸法精度を得られないため注意が必要です。
プラスチック(樹脂)の種類について
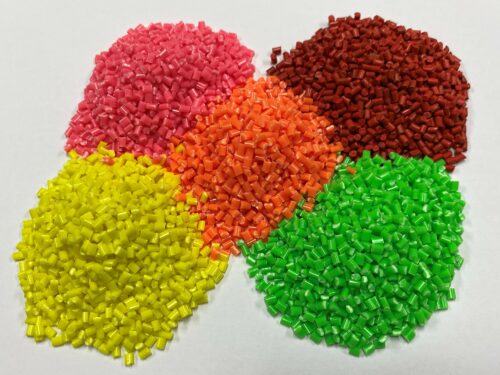
プラスチックの材料は大きく分類すると2種類あり、それぞれにメリット・デメリットや特性が異なります。
熱硬化性樹脂
熱硬化性樹脂は、加熱前は流動性を持っていますが、熱を加えることで固化するプラスチックのことです。たわみや歪みに対して強いなど機械的特性に優れており、耐熱性や耐薬品性が高いのがメリットです。一方、成形時間が長くコストがかかるというデメリットがあるため、使用環境が限定された要求性能の高い製品に多く使います。
代表的な熱硬化性樹脂は、電気・電子機器やブレーキ摩耗材に使用されるフェノール樹脂や、半導体封止材のエキボシ樹脂、接着剤や配線器具のユリア樹脂、食器・化粧板のメラミン樹脂、浴槽の不飽和ポリエステル樹脂などがあります。
主な成形方法
成形における特徴
熱硬化性樹脂の成形方法としては、コンプレッション成形やトランスファー成形が一般的です。これは、材料を加熱すると一旦は液状化しますが、次第に化学反応により固化するため、温度管理が難しいというのが関係しています。
一般的に材料の投入量は一定ではなく、余分に出る材料によりバリが出やすい特徴があり、バリ処理が必要です。また、固化する途中でガスが発生するため、金型からガスを抜く工程を行うことがあります。
熱可塑性樹脂
熱可塑性樹脂は、加熱前は固形で、熱を加えると柔らかくなり流動性を持つようになるプラスチックです。冷却すると固化し、加熱すれば再び軟化する特徴を持ちます。成形時間が短くコストパフォーマンスに優れているので大量生産に向いており、多くのプラスチック製品に使われるのが熱可塑性樹脂です。その反面、機械的特性に劣ります。
代表的な素材は、包装フィルムや容器・日用品に使用されるポリエチレンや、包装フィルム・自動車部品などのポリプロピレン、給排水管や電線の被覆材などのポリ塩化ビニル、透明ケース・保温容器のポリスチレン、照明器具・看板などのポリメタクリル酸メチルなどがあります。
主な成形方法
成形における特徴
熱可塑性樹脂は熱を加える時間が長くても変質しないため、ほとんどの成形方法に対応できます。成形の過程では高速・高圧でプラスチック材料を金型に充填することが欠かせませんが、薄肉にしやすいため軽量化が図れます。形状が複雑な製品にも対応し、何より低コストで製造できるのが特徴です。
代表的なプラスチックの成形方法(加工方法)とは?
プラスチックの成形方法はさまざまなものがありますが、金型を使うのはどれも共通している点です。ここでは代表的な成形方法をご紹介します。
射出成形
プラスチック成形としては代表的な加工方法の一つです。熱を加えて溶融させた材料を金型の中に流し込んで保圧・固化させる成形方法であり、複雑な形状のものでも比較的短時間で成形可能です。
出来上がりの寸法精度も高く、バリ取りなどの加工もほぼ不要であることも特長と言えます。ただし材料の温度や圧力、金型の設計などは高度な技術・ノウハウが必要でもあります。
※参考記事:射出成形について
インサート成形
インサート成形とは、板金やネジ、ICチップなどのインサート部品とプラスチックを一体に成形する加工方法です。金型が開いた状態の時にインサート部品を挟み込み、そこへ溶融させた材料を流し込んで一体成形させます。
金型の設計は高度な技術が必要ですが、組み立て工程を必要としないため、工数削減や機能性のある部品を付与できるのがインサート成形のメリットです。
※参考記事:インサート成形について
押出成形
ホースや包装フィルムといった同一断面で、長尺のプラスチック製品を成形する方法です。断面形状と同じ形をした金型に材料を流し込み、押込みながら連続的に成形していきます。
長尺のホースやパイプ、シートでも小さく安価な金型で作れるためコストパフォーマンスに優れているほか、高い生産効率を誇ります。ただし、加工精度は低く、少量生産には適していません。
コンプレッション成形(圧縮成形)
熱硬化性樹脂としては一般的な成形方法で、金型にあるキャビティに材料を流し込みプレスさせて固化させます。型を閉じながら成形するため寸法精度は高くなく、浴槽や洗面化粧台など大型で肉厚な製品に使用される成形方法です。
トランスファー成形
こちらも硬化性樹脂でよく使われる成形方法です。ポットの中で材料を溶融させてキャビティに移送してから硬化させる仕組みです。
予熱工程があるため硬化時間を短縮できるほか、型を閉じてから硬化させるので寸法精度が比較的高いのが特徴です。ただし、金型に残ったカルを毎回取り除くので材料の無駄ができるのがデメリットと言えます。
\ 図面は不要!たった1分で完了! /
プラスチック(樹脂)のメカニズム・工程
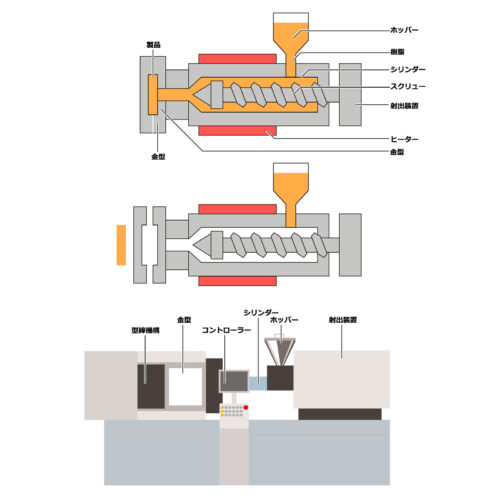
プラスチックはどのような工程を経て成形されるのでしょうか。ここでは射出成形の工程について解説します。
STEP1.型締め・射出
初めに成形機の上部にあるホッパーへ材料となるペレットを投入させます。金型を閉じてからシリンダ内部にペレットが送られ、スクリューで前進させながらヒーターで加熱・溶融させます。スクリューで混ざりあった材料は金型のキャビティへ高圧で注入。
STEP2.保圧・冷却
金型の中でプラスチックが固化するまで圧力を保ったまま保持します。冷却されると少し収縮する成形品にわずかなプラスチックを補充することもあります。
STEP3.可塑化・型開き
プラスチックの材料となるペレットをシリンダ内部で200~300℃に加熱させ、次の成形品のために溜めておきます。金型の可動側ダイプレートを動かして金型を開きます。
STEP4.製品の取り出し
金型を開いて製品を取り出します。この際にゲートはカットしておきます。成形品が傷つかないように、ロボットアームなどで取り出すことが一般的です。このサイクルを繰り返して大量生産するのが射出成形の仕組みです。
プラスチック(樹脂)の成形における注意点
プラスチックを成形する際は、材料選びなどの製品設計が重要なことはもちろん、製品によってどの成形方法が適しているかを考えていく必要があります。一般的なプラスチックの成形における注意点を見ていきましょう。
注意点①:製品設計
製品設計の段階では、どのような性能が必要かはもちろん、材料や成形方法を選ぶことも大切です。プラスチック材料には機械的特性や熱特性、電気特性、化学特性など様々な特性があり、作りたい製品にはどのような特性が要求されるかを考えて材料を選ばなければなりません。候補材料の物性データを確認して、変形のしにくさや割れにくさといった要求特性に合った材料を候補にしていきましょう。
注意点②:金型設計
高い寸法精度を確保するには金型の設計がとても重要です。プラスチックは温度変化に影響を受けやすく、成形の段階で加熱から冷却をすると温度が低下することで少なからず収縮します。金型設計での注意点は、このときの収縮率を計算することです。
(詳しくはこちら:寸法精度を求めるときは、切削か射出成形)
出来上がりの製品は金型よりも多少は小さくなりますが、あらかじめ収縮率を考慮して金型を設計しないと目的の製品になりません。収縮率は材料や成形条件によっても異なるため、熟練の技術が必要です。
注意点③:成形条件
プラスチックを設計通りに成形するために、成形におけるさまざまな条件をコントロールしなければなりません。代表的な成形条件には、樹脂や金型の温度、充填圧力、保圧、冷却時間などがあります。
例えば、充填圧力が高すぎると製品にバリが発生します。その他に冷却時の収縮により発生するヒケと呼ばれる凹みや、ウェルドラインと呼ばれる気泡なども適切な成形条件でなければ起きるため注意が必要です。
PlaQuickの成形事例
PlaQuickではさまざまなプラスチック成形品の試作を請け負っています。設計〜試作〜検討までの流れを低コストかつ、ス ピーディに行うことが可能であり、これまで多数の実績があります。
ケース①:「ORPHE(ウェアラブル)」
株式会社ORPHE社が提供するスマートシューズ「ORPHE」は、履くだけでランナーの「着地法」「プロネーション」「ストライドの長さ」「ピッチ」「接地時間」を計測できるシューズです。
こちらの製品には、PlaQuickの射出成形が採用されています。センサーモジュールの筐体や軽く丈夫な樹脂製のソールパーツを製造。PlaQuickでは図面提供から製品確認まで素早く行うことで、開発スピード向上に貢献しています。
※参考記事:スマートシューズ「ORPHE」の事例
ケース②:「光岡自動車(車)」
デザイン性あるファッションカーを生み出す株式会社光岡自動車。創業50周年記念モデル「ロックスター」の開発にも、PlaQuickの射出成形が採用されています。
当初、光岡自動車ではヘッドライトユニットを自社で試作していましたが、手作りでは時間がかかり品質も一定ではないという問題がありました。PlaQuickでは3Dデータからダイレクトに試作品を提供することで、金型費用の削減や工期短縮に貢献。量産で使用するPPのグレードもPlaQuickで用意することで、機能評価に役立てることに成功しています。
※参考記事:光岡自動車の事例
プラスチック(樹脂)の成形ならPlaQuick
プラスチックから目的通りの成形品を作るには、材料選定から金型設計、コストなどさまざまな課題があります。
PlaQuickでは、製品の特性に合わせたプラスチック材料を調達できるほか、量産品と同じ条件での試作品を低価格で提供できます。プラスチックの成形をお考えの方は、PlaQuickでの試作を一度検討してみてはいかがでしょうか。
\ 図面は不要!たった1分で完了! /